あなたの現場でこんなお悩みありませんか?
あなたの現場で
こんなお悩みありませんか?
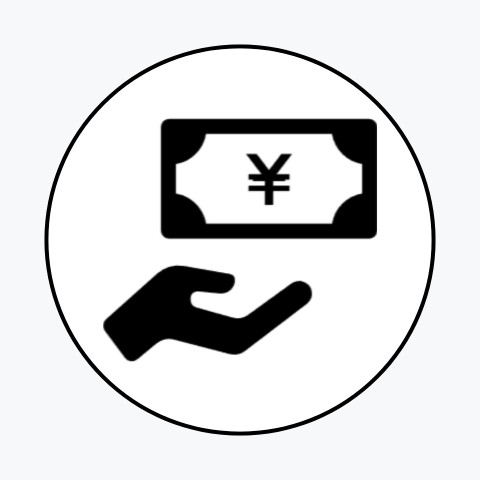
バッテリー交換100万円以上と高額
想定外の出資が突発的に発生
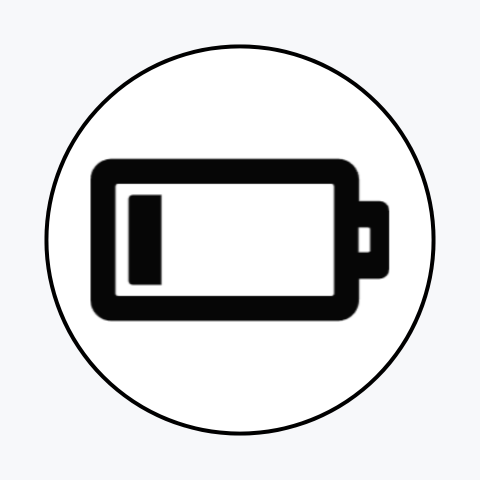
バッテリー容量の減りが早く
作業が途中で止まる恐れがある
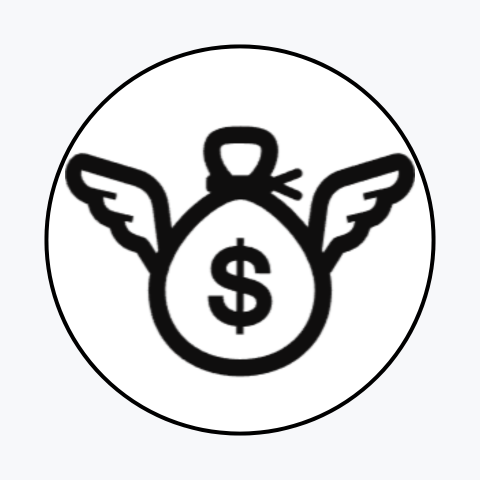
単セル交換したものの半年で劣化
投資が無駄だったと感じる
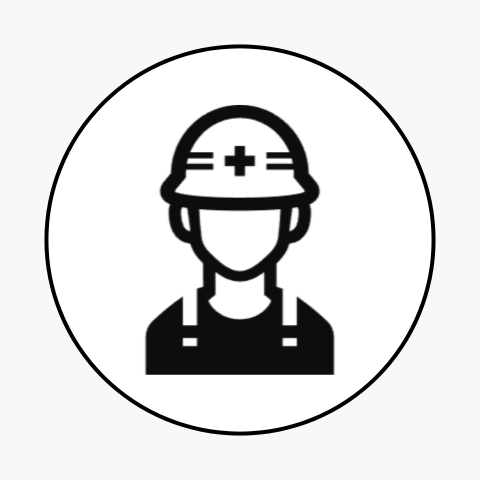
車両台数が少なく
1台の不稼働車両が要因となり
作業効率に大きく乱れが生じる
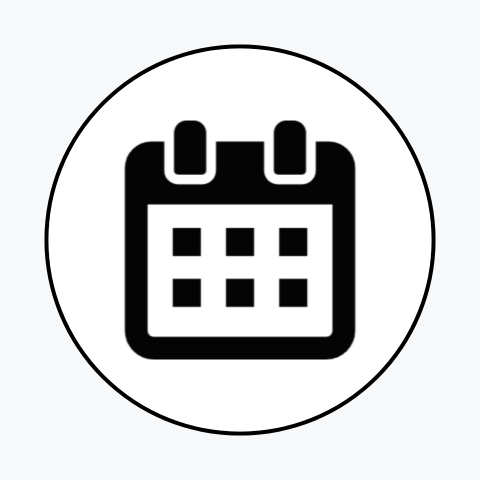
バッテリー5年交換サイクルと計上したが、
短期間の交換が必要となり
すでに予算オーバーしている
どの現場でも避けられない「バッテリーの悩み」
どの現場でも避けられない
「バッテリーの悩み」
CASE1 イワシやサバを運ぶ水産加工企業のケース
1日14時間稼働によりバッテリーの寿命が短い
CASE1
イワシやサバを運ぶ水産加工企業のケース
1日14時間稼働によりバッテリーの寿命が短い
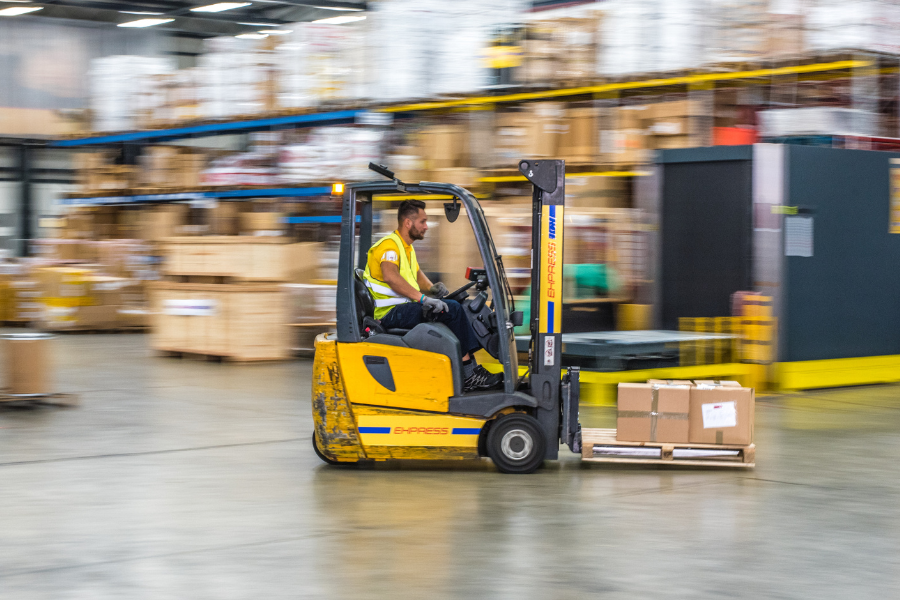
明治時代に創業し、現在は6代目が運営する水産加工業の本企業は、銚子港の近くに位置し、毎日のように新鮮なイワシやサバを水揚げし、自社で買い付け・選別・凍結保管・加工・販売までを一貫して行っています。銚子港は、2011年から2022年まで12年連続で全国の水揚げ量No.1を誇る漁港であり、海の恵みが豊かな土地柄です。しかし、近年は漁獲量の減少があり、その影響を受けながらも、変わらず新鮮で高品質な水産物を届けています。
このような業界特性の中、現場では、スピードと鮮度が命。特に冷凍庫内(-35℃)で稼働するフォークリフトの重要性が高く、最大10台のフォークリフトが1日13〜14時間という過酷な条件で稼働し続けています。特に大型冷凍車両やカプセル型フォークリフトは、温度管理や荷重に対して非常に高い負荷がかかるため、バッテリーの劣化が進行しやすく、業務に支障をきたしていました。
その中で、バッテリーの寿命が限界に近づき、昼休みに補充電をしないと業務がフル稼働できない状況が続いていました。バッテリーは48V730Ahや80V470Ahの大容量タイプで、1台あたり200万円前後と高額なため、頻繁な交換は経営的に難しく、バッテリー寿命を延ばす方法を強く求めていました。
サービス導入後、これまで補充電なしでは終日使用できなかったバッテリーが容量回復し、補充電なしでも終日使用できるようになりました。使用後の残容量メーターは、終業後に残り2コマから7コマに改善され、繁忙期でも安心してフル稼働を維持できるようになりました。
これにより、昼休みに補充電をする手間がなくなり、業務効率が大幅に向上しました。また、車両管理者からの依頼を受け、現場で全20名のオペレーターに向けた15分間のバッテリー運用説明会を実施。休憩時にこまめに補充電を行うことや、残容量メーターを5/10コマ以上に維持する運用方法を指導しました。これにより、スタッフ全員が一貫した運用方法を守り、より効率的な運用が実現しました。
さらに、車両メーカーから「寿命」と診断されていたバッテリーは、診断後3年半経った現在も元気に稼働しており、新たなバッテリーの購入は不要となりました。この結果、大きなコスト削減が実現し、経営面にも良い影響を与えました。バッテリーの交換費用を抑えることができ、資金繰りの安定にもつながっています。
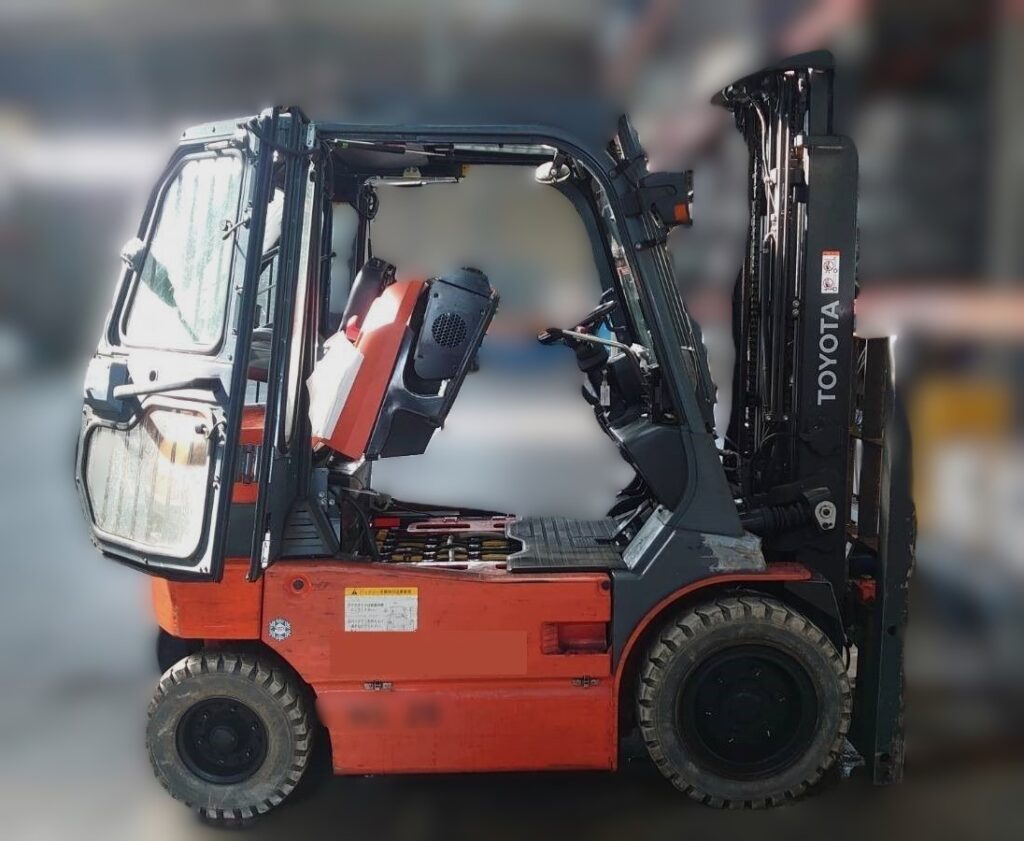
CASE2 航空宇宙部品加工業を手掛ける企業のケース
低負荷稼働だが、寿命がわずか3年にとどまる早期劣化が発生
CASE2
航空宇宙部品加工業を手掛ける企業のケース
低負荷稼働だが、寿命がわずか3年にとどまる早期劣化が発生
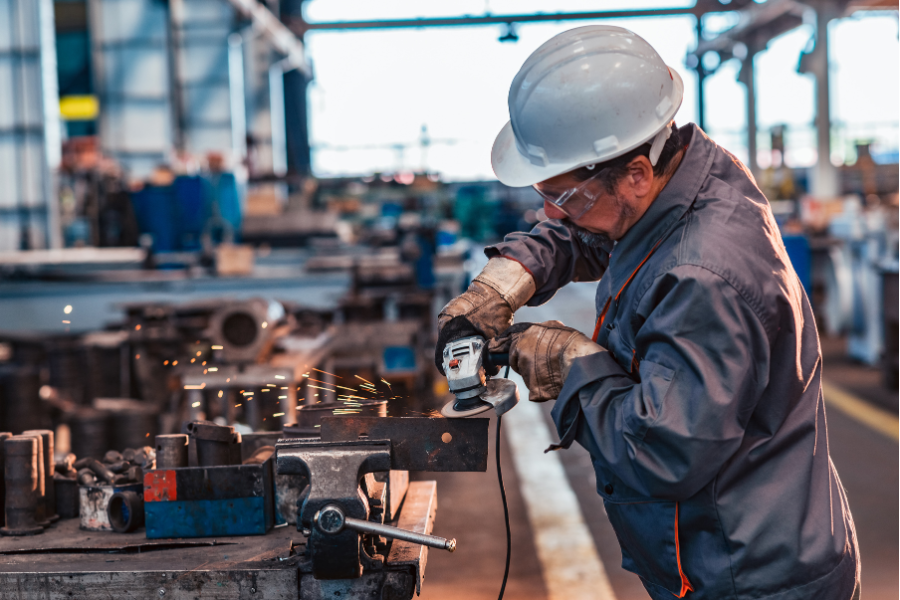
本企業は、茨城県に本社を構える精密部品加工メーカーです。航空機やロケットなど、厳しい精度が求められる分野で数多くの製品を手がけ、50年以上にわたりものづくりの現場を支えています。チタンやインコネルなどの難削材にも対応できる加工技術は業界内でも高く評価されており、その確かな品質は国内外の最先端機器に活かされています。
こうした高度な製造を支える工場では、2.5トンカウンター式フォークリフトが使用されています。工場は24時間体制で稼働している一方で、フォークリフト自体の1日あたりの稼働時間はおよそ3時間と短めです。しかし、入出荷のタイミングが日々異なることから、まとまった充電時間が取りづらく、補充電のみの運用が続いていました。
また、その運用方法がバッテリーにあまりよくない影響を与える可能性があることを知らず、結果的に565Ahの大型バッテリーが3年未満で寿命を迎える状況が発生していました。その費用は1台あたり約130万円と高額でした。「思ったよりも高い」というコスト意識は現場でも強く、稼働時間の短さとは裏腹に、バッテリー交換が経営的な課題の一つとなっていました。
弊社の製品を導入後、まず現場で実感されたのはメーター残量の変化でした。導入から2か月後には、オペレーターより「メーターの減りが遅くなった」との声が上がり、10コマの状態からメーターがほとんど減らなくなったという体感が共有されました。設置から4年1か月が経過した現在でもバッテリーの劣化症状は見られず、従来の交換サイクル(3年未満)を大きく超えて使用が継続できており、稼働は安定しています。
この効果を維持するため、弊社では導入後すぐに運用面のアドバイスを実施。補充電のみだった充電運用を見直し、週に2〜3回のフル充電を実施いただくよう提案しました。あわせて、現場スタッフへの充電管理に関する教育も実施。その結果、比重値は設置から2か月で改善。4か月時点では一時的に劣化が進行したものの、これは「劣化が改善されたことで気が緩んでいた」との工場長の声を受け、営業による再フォローで再び運用が定着しました。
結果として、バッテリーの寿命延長によって年間のコストが大幅に削減され、企業は「初めて3年を超えて使えるようになった」と、その効果に驚きを隠せませんでした。
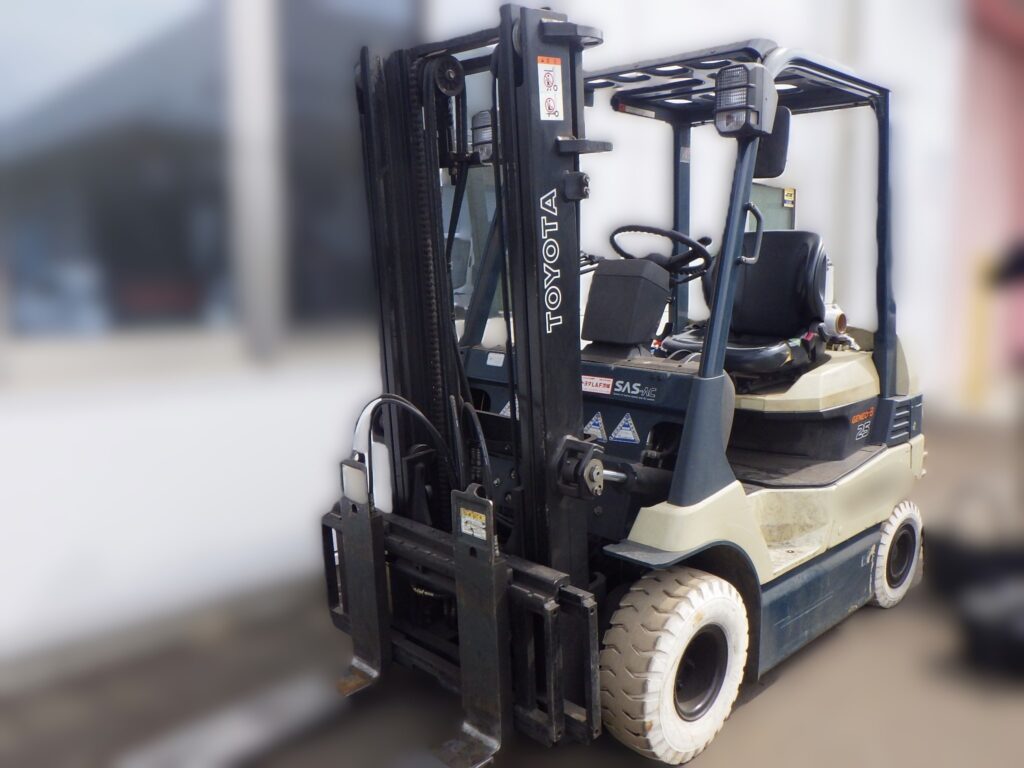
5社のお悩み改善ストーリーをチェック >>
なぜバッテリーはすぐ劣化するのか?
そこから始まる最適解
最大の原因は「バッテリー管理が行われていない」こと
訪問した企業のうち、バッテリー管理を行っている企業は約3割にとどまります。ほとんどの現場で、バッテリーの劣化を早める運用が日常的で、本来よりも早く寿命を迎えています。
バッテリー管理を行わず、過放電や過充電、不適切な補水タイミングなどの誤った運用を続けることにより、バッテリーの性能低下が進行し、結果的に交換コストの増加につながります。
当社で最も重視しているのは、お客様の運用環境です。フォークリフトの稼働状況やバッテリーの特性を詳細に分析し、適切な管理方法を提案。導入時には、管理者だけでなくオペレーターにも運用のポイントをレクチャーし、不適切な使用による劣化を防止します。
また、導入後も定期的なバッテリー診断を実施し、オペレーターへのヒアリングを通じて、実際の使用状況を把握。単なるデータ上の分析ではなく、稼働量の変化や充電習慣などの実態を考慮しながら、バッテリーの性能を最大限に引き出せる運用を継続的に支援します。
正しい運用を習慣化することで、バッテリーの寿命を延ばし、運用コストの削減と安定したフォークリフト稼働を実現します。
もう一つの原因は「バッテリー劣化対策の不在」です
多くのお客様は、バッテリーの劣化を防止する装置をご存じありません。劣化防止装置はバッテリーの劣化速度を緩やかにし、またバッテリーの劣化を回復させ、新品状態を維持する装置です。
IchouSystemは、特殊パルスを電極板に流すことによって、バッテリーの劣化の原因である硫酸鉛被膜の付着を防止し、分解・除去します。この技術により、バッテリー内部をクリーンな状態に保ち、容量の回復と劣化の防止を実現。結果として、バッテリーの寿命を大幅に延ばすことが可能になります。
バッテリー管理のための
運用アドバイス
オペレーターへのヒアリングとバッテリー計測データをもとに、バッテリーの状態を正確に診断し、最適な運用方法をご提案。独自のノウハウを活かし、効率的かつバッテリーに優しい運用をサポートします。統一された指針のもと業務効率を最大化し、バッテリーの寿命延長を効果的に実現します。
バッテリー劣化対策は
延命装置 「IchouSystem」
IchouSystemは、バッテリーに直接取り付けて劣化の原因となる物質を分解し、性能の維持・回復を実現します。これにより、バッテリーの寿命を1.5倍~2倍に延ばすことが可能です。
コラム:鉛バッテリー「劣化」の仕組み
バッテリーの劣化原因の約90%は、正極板の格子部分に硫酸鉛が膜状に付着することに起因します。
この硫酸鉛は、放電時に電解液(希硫酸)と電極板(鉛)が化学反応を起こして生成され、充電時には外部からの電力によって分解されます。
しかし、充電の過程ですべてが分解されるわけではなく、一部が電極板に残留し、繰り返される放電・充電サイクルによって蓄積していきます。正極板の格子に硫酸鉛被膜が付着し、格子表面を徐々に覆うことで、電気の通り道が狭まり、電気の流れが阻害されます。
そのため、電気を蓄える能力が徐々に低下し、バッテリー容量が減少します。こうした劣化が進行すると、最終的にはバッテリーが寿命を迎え、使用不能となります。
コラム:鉛バッテリー「充放電」の仕組み
鉛バッテリーは、鉛(Pb)と酸化鉛(PbO₂)、そして希硫酸(H₂SO₄)を利用した化学反応でエネルギーを蓄積し、必要に応じて電力を供給します。
その仕組みは、充放電のサイクルを通じて効率的にエネルギーをやり取りすることにあります。
放電時には、負極板の鉛(Pb)が希硫酸と反応して硫酸鉛(PbSO₄)となり、同時に正極板の酸化鉛(PbO₂)も硫酸と反応して硫酸鉛になります。この化学反応により、外部回路を通じて電子が移動し、電力を供給します。このとき、電解液中の硫酸濃度が低下するのが特徴です。
一方、充電時には外部電力を用いて化学反応を逆転させます。これにより、硫酸鉛が再び鉛と酸化鉛に戻り、電解液中の硫酸濃度が回復します。
このサイクルにより、鉛バッテリーは繰り返しエネルギーを蓄え、安定した電力供給を可能にします。
バッテリー運用改善のお問い合わせ
資料をダウンロードする
サービスが提供する3つの価値
運用コストを最大86%削減
バッテリーの寿命を延ばすことでコスト削減を実現します。一般的に80万円~200万円かかるバッテリー更新費用を最大86%削減できるため、設備投資の負担を軽減され、利益率の向上につながります。
また、バッテリー交換費用と新車購入費用に大差がないため、バッテリーの寿命タイミングに車両ごと更新されている場合は、延命によるコスト削減効果はさらに大きくなります。
低下した生産性を大幅改善
バッテリーの劣化により「終日使用ができない」「爪がスムーズに上がらない」といった問題が発生すると、作業の遅れや業務の非効率化を引き起こします。IchouSystemがバッテリーの性能を回復し、従来の稼働時間や操作性を取り戻し、現場の生産性向上とスムーズな作業環境を実現します。
CSR・SDGs活動への貢献
バッテリー寿命を延ばすことで廃棄物削減と資源の有効活用が実現し、環境負荷を低減します。これにより、SDGs目標12(つくる責任、つかう責任)や目標13(気候変動対策)に貢献し、企業のCSR活動としても評価されます。
IchouSystemの導入効果
-体感と数値で証明可能-
導入後の改善は「体感」と「数値」で確認可能
導入後の改善は
「体感」と「数値」で確認可能
オペレーターが体感できる改善効果
実際に現場で使用するオペレーターからは、次のような変化が報告されています。
・夕方の残量メーターが増えた
・パワーダウンしなくなった
・終日持つようになった
これらの変化は、バッテリーの回復によって使用できる容量が増加し、充電効率が向上した結果です。
数値で知るバッテリーの改善効果
バッテリーの容量を示す指標として、比重値が使われます。比重値とは、バッテリー内部の電解液(希硫酸)の濃度を示しており、容量があとどのくらい使用できるのかの指標になります。比重値の初期値は1.28であり、放電が進むと比重値が低下し、充電すると比重値は上がり、もとの1.28に近づきます。バッテリーの劣化が進行していると、容量の減りが早くなるため、比重値の減りも早くなることがあり、また充電を普段通りにしても1.28まで上がらないこともあります。
オペレーターが劣化改善を体感した事例
CASE1<補充電をせずに終日使用が可能になった事例>
CASE1
<補充電をせずに終日使用が可能になった事例>
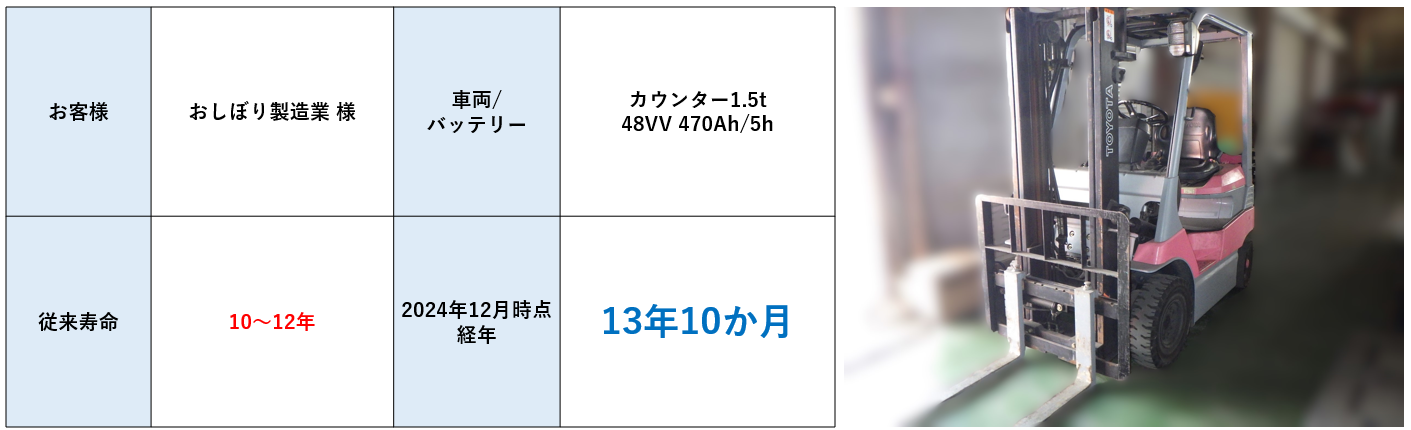
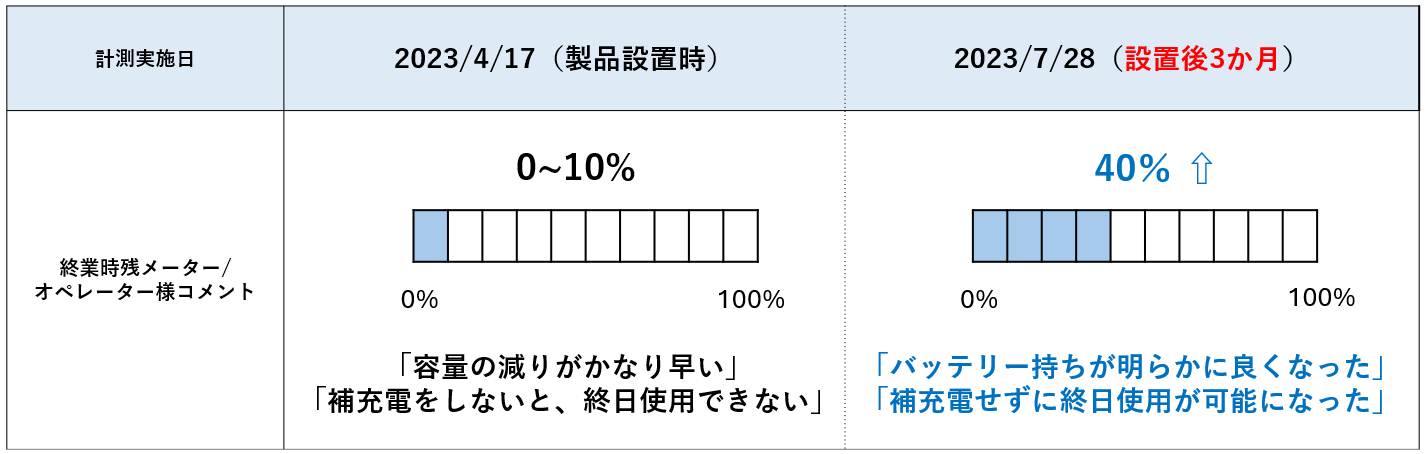
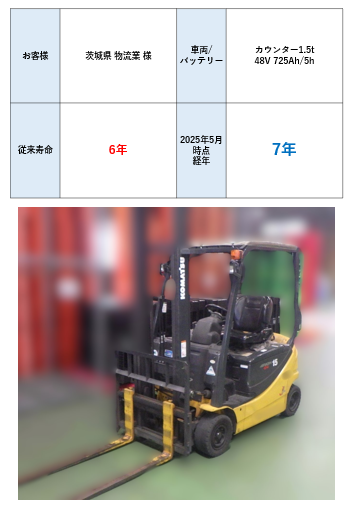
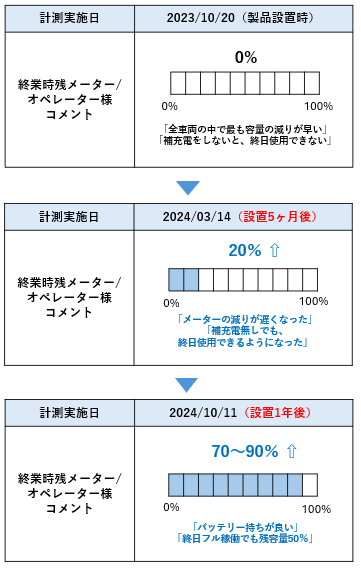
CASE2<バッテリーの容量が70%以上回復した事例>
CASE2
<バッテリーの容量が70%以上回復した事例>
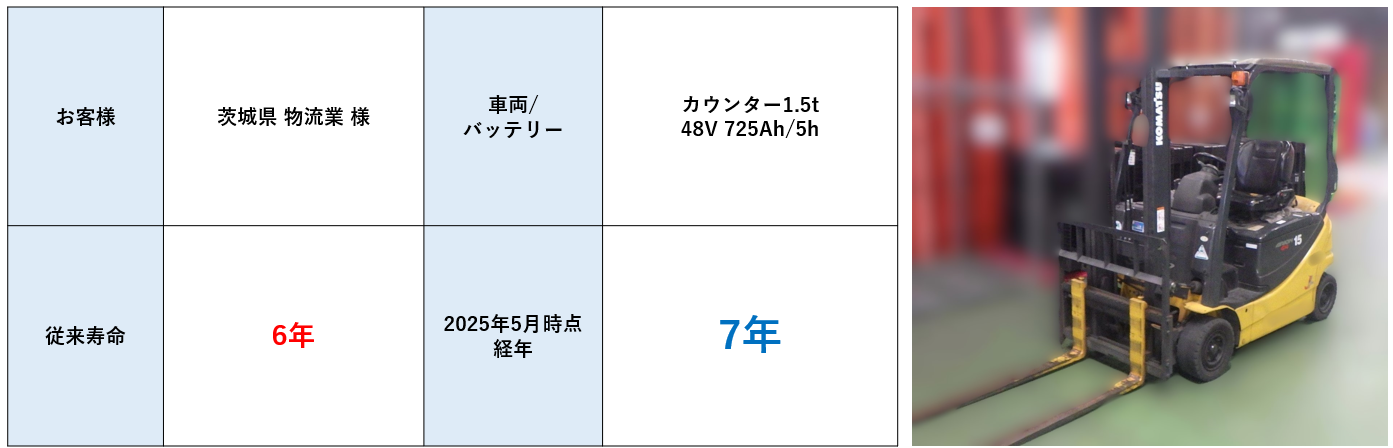
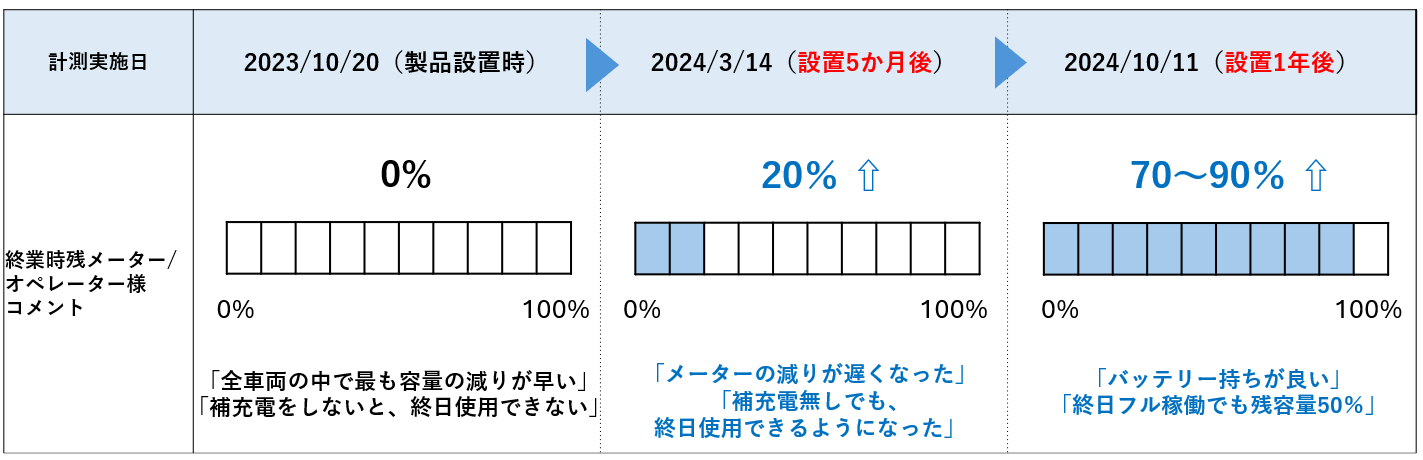
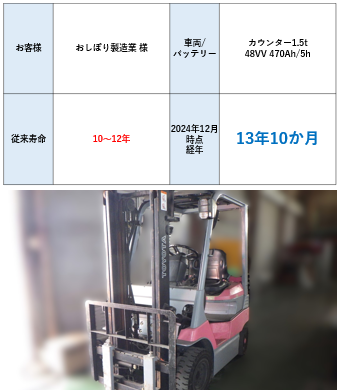
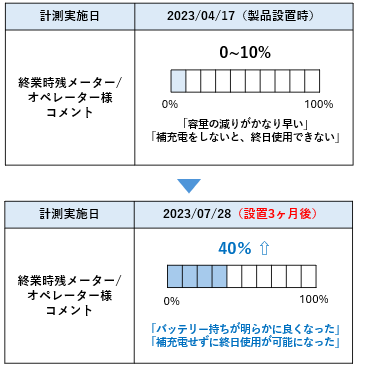
劣化改善支援のお問い合わせ
資料をダウンロードする
IchouSystemが選ばれる
4つの特徴
特徴➀実績に裏打ちされた信頼の技術
300社以上の導入実績を誇り、各現場で信頼のバッテリー延命技術を提供しています。成功事例に基づき、企業のコスト削減と運用効率を大幅に改善し、多くの企業様にご満足いただいています。
特徴②特許取得&公的認証の高信頼性
当社の技術は特許を取得し、業界での独自性と新規性が認められています。さらに、国土交通省が運営するNETIS(新技術情報提供システム)に登録されており、公共事業でも採用可能な信頼性が証明されています。また、徳島工業短期大学で実施された実証実験によって、その効果も実証済みです。
特徴③現場環境に合わせた運用サポート
バッテリーは誤った方法で使用すると寿命が半減してしまいますが、弊社が持つバッテリーに関する豊富な知識や経験を活かし、車両の使用状況や劣化状態に応じた最適な運用方法をご提案します。さらに、導入後も定期診断サービスによって、運用が適切に行われているか、使用感や操作状況に変化がないかを確認し、必要に応じて改善点をアドバイスすることで、ほぼ100%の確率で延命を実現します。
特徴④事前診断でミスマッチを防ぎ、安心導入
当社の事前診断では、バッテリーが延命可能かどうかをまず確認し、延命不可の場合にはその旨を明確にご報告します。延命可能な場合は見込まれる延命期間や運用改善が必要なポイント等を詳しくご説明します。これにより、導入後のリスクが軽減し、無駄なコストやトラブルを避けることが可能です。
サービス導入の流れ
1.お客様からご依頼
製品についての説明や見積書、事例について詳しく知りたい方は、お問い合わせフォームよりお問い合わせください。
2.お客様の課題をヒアリング
お問い合わせから1営業日以内に担当者からお電話にてご連絡いたします。
お客様がお持ちのフォークリフトの車両やバッテリー情報や今後のスケジュールについてお電話でお話いたします。
※無料です。
3.製品使用上の注意点
オンラインにて製品の仕組みや効果、事例、お見積り、製品取り付け時の注意点などをご説明いたします。点検簿があるとより具体的なご説明が可能です。
※無料です。
4.現地調査
バッテリー計測(1台当たり20分)を実施し、取り付ける製品を確定させていただきます。
※実費のみ(交通費のみ)ご請求いたします。現地調査なしに御見積書を提出することも承ります。
5.御見積書のご提出
製品取り付け前の最終確認やお見積もりについてやり取りさせていただきます。
※無料です。
6.製品取り付け工事の実施
取り付け作業及びバッテリーの計測を実施します。1台当たり40分程度で完了します。現場業務に支障が出ないよう、ご都合の良い時間帯に合わせて作業対応いたします。
バッテリー運用のお問い合わせ
資料をダウンロードする